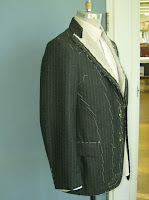
This is the baste up of jacket number 8, nice wool, the fitting went well, I don't know what possessed the sewer to make up a finished collar for a basted jacket, so I guess she'll be doing that again. It's the little things like that, working with people you don't usually work with and the communication misunderstandings that can make you crazy sometimes.
Overwhelmed is how I am feeling.
Yes, it is getting down to the wire and there's no time to spare.
I asked for and got 2 extra sewers this week. Hooray, now I am supervising 7 people. That's extra work in itself- especially with people who aren't that familiar with the way I like to work.
My goal for last Friday was to have everything cut out, so I could move on.
At 6 o'clock on Friday, I cut the last pattern piece of the second footman's tailcoat, but I didn't get the linings cut out. Close but not quite done.
The real kicker though, the one that is making me more overwhelmed, is that one of the actors has been working out and dieting- you know every so often someone will come for a fitting and say they're going to lose a few pounds and they rarely do, but this time, he did. Well, he's actually gone down a bit more than a full size. Three inches smaller in the waist. Two inches off the hips and chest.
You know, I cut his trousers out over 6 weeks ago and they were nice and they were finished and hemmed and at 6 o'clock today, I was drafting a new trouser pattern to make new tux trousers and unpicking the suit trousers because I don't have any more of the fabric to cut new ones.
I can't even begin to talk about altering the jackets. I think I'll sit and stew about it a bit more.