I thought there was an extra week in November and I was really disappointed to find out I was wrong!
I have been very busy and the phone has been ringing off the hook, in fact I turned down a project because I just couldn't add one more thing to the list. Anyway, I am trying to keep up with blogging.
So, I recently made a toile for an opera costume and fit it. It is quite a challenge to fit disproportionately larger body types for a number of reasons. One is that people do not get larger with any kind of controlled change. Each person gets larger in their own unique way.
I have to rely less on standards and more on modifying my basic drafting to interpreting the person's
shape from photos that are provided. One other challenge is the pattern shapes change in ways that you may not be used to: the pattern no longer looks proportional. I often find too, that men's wear gets a bit more challenging because there are fewer accepted style lines and darts than in women's wear.
This project reminded me of something I made earlier this year: a body padding for Falstaff.
It is never easy to make a body padding nor to wear one.
The actor and designer had a definite take on the shape they were after, and what they didn't want, and it was my job to create something. (in much too short a time, I may add)
They wanted a more realistic take on what had been done here in the past.
Right.
What has been done in the past? Well, everything from layers of batting hand stitched layer upon layer to an inner base, which could be as simple as a t-shirt with a small "belly" added, to a full unitard with combinations of rigilene frameworks and small crescent shaped bags of Lycra filled with styrene or plastic beads.
They wanted the padding to act like real flesh, compressible to an extent and be more realistic looking.
OK.
I decided to try to work with memory foam. I had never worked with it before and we had a difficult time sourcing what we needed in a short time frame.
I wish I had taken photos of the whole process, but it was so busy and this show had a very "organic" approach to it, that I barely had time to think at all. Sigh.
I started with a base of fine power net/Lycra.I knew I was going to have to build up the arms and legs, so I made a pattern for a close fitting bodice and a shorts. This way I had a waist seam where I could adjust the fit if needed. I fit the base on the actor first. In the fitting the designer and I drew on it indicating key areas that I could reference once I was back at my table. I took quite a few measurements as well, and we tried to establish a final chest and waist size to aim for.
I returned to my room and then adjusted a stand to be more like his natural shape so that we had a reference point from which to build on. This was so important because we couldn't be making major changes in the actual fittings with the actor.
I began with my own sketch of a body shape, and figured out what attributes of that shape I could try to reproduce. I have to say that this is where my early training in life drawing painting and sculpture comes in handy.
I started with the belly, using some air conditioner foam to build up a bit of solid understrucure.
I then built up and created rolls of fleshy areas with memory foam. We punched holes in the foam wherever possible to allow a bit of air flow through to his body. These areas of foam often consisted of two or three layers or blocks of foam that had a larger piece laid over top and wrapped to create three dimensions. We glued the under blocks in place as well as the wrapped edges with plain old white glue which seemed to do the best job of the many glues we tried.
Those foam shapes were then were covered in another lightweight power net/Lycra which gave us the means to attach the rolls to the base layer or to another roll. The pieces were kept separate to simulate how I thought real flesh would behave. So, there is an overhang/apron of foam in the abdomen and another at the waist. this allowed the actor to wear his trousers waist up under the belly roll if he wanted. The chest padding was separate as was the shoulder blade area. The arms and legs and seat were also padded up.
It took a lot of time to figure out and make, as I was also busy with the rest of the show and finishing up the previous shows. We proceeded in stages, I would figure out a shape, hand it off to Karen to glue and cover. Sometimes the shape is not quite right and we had to modify the chest by adding in a piece of foam covered separately, as we didn't have time to re cut and recover that section.
Once the padding was finished, we could then start on the clothes.
I confess that I just draped the clothes right on the stand rather than try to draft and work it out as a flat pattern. Draping just seemed more immediate and time was of the essence by then.
I found out in a fitting after it was finished that they wanted him to appear in a set of long underwear over this padding and I just about fainted! I mean the foam we were able to get was green and pale blue, and what was that going to look like? would it show through? Could we get long underwear on short notice that covered the padding properly? Of course we ended up making a set of long johns and Henley. At that point the actor wanted some "anatomy" made for realism's sake, which needed to be removed at one point (they gave him tight jeans to wear at one point and there wasn't enough room) so we made him a "package" using the Lycra and styrene beads, and it was a complicated bit of business figuring out how to make that work.
Oh our work is never dull, I tell you!
Sunday, December 18, 2016
Sunday, November 20, 2016
waistcoats on the bias
I am making some suits for a show and the designer has designed the waistcoats to be cut on the bias.
OK, I think- or rather I didn't really think about it much at first- no problem.
I know it isn't really an impossible task, but it is time consuming and it is always hard to judge how much more time consuming until you are in the midst of it.... So lets break it down.
The basics:
Firstly- the design is a 1930's double breasted waistcoat with a laid on collar/lapel.
The cloth is a windowpane check. White on black. The windowpanes are rectangles not square.
Challenge: Bias- it stretches, so it needs control.
Solution: fuse straight grain fusible interfacing onto bias fabric.
Challenge: the true bias on a pattern with rectangles gives no happy visual location for the CF line.
Solution: draw a line through the corners of the rectangles and use that as a CF line, so it is not on the true bias.
Challenge: a traditional vertical dart in front will not be a good choice as it will distort the look of the "bias"
Solution: close out the front dart and transfer it to the neckline where it will eventually be covered by the collar.
Challenge: which grain to cut the collar? With the neckline dart, the laid on collar will never be able to match the fabric of the body. It can only match up to the dart, the worry is that it will just look like a mistake.
Solution: cut the collar/lapel so it is a contrast grain so the windowpane contrasts with the body- make a detail out of it.
Challenge: applying the fusible to the wool, making sure the right and left fronts are mirror images. dealing with shrinkage that comes with fusing.
Solution: Use a fusible that is somewhat translucent so I can see the windowpanes through it.
Draw out the pattern pieces on the fusible giving a clear CF line.
Block out the fabric in a single layer at the ironing table using a metre stick and a square, so the windowpanes stay square and true.
Chalk the pattern pieces onto the wool. including a clear CF placement line.
Apply the fusible to the wool carefully maintaining the alignment of CFs and overall placement.
Fuse one front, re block wool, chalk other front, and repeat making sure the alignment of the other front is a mirror image of the first.
At this point, the pieces are rough cut and I have to take them back to the table and check and redraw the pattern, because fusing always shrinks slightly.
Do the same process for the lapel/collar pieces.
Repeat for the second vest which must match the first.
This is the idea, partially done and placed roughly in position. We are going to put the welt pockets on the straight grain to match the lapels.
I think it will look very striking once it is finished, but oh boy it took a lot of time to get them cut out!
OK, I think- or rather I didn't really think about it much at first- no problem.
I know it isn't really an impossible task, but it is time consuming and it is always hard to judge how much more time consuming until you are in the midst of it.... So lets break it down.
The basics:
Firstly- the design is a 1930's double breasted waistcoat with a laid on collar/lapel.
The cloth is a windowpane check. White on black. The windowpanes are rectangles not square.
Challenge: Bias- it stretches, so it needs control.
Solution: fuse straight grain fusible interfacing onto bias fabric.
Challenge: the true bias on a pattern with rectangles gives no happy visual location for the CF line.
Solution: draw a line through the corners of the rectangles and use that as a CF line, so it is not on the true bias.
Challenge: a traditional vertical dart in front will not be a good choice as it will distort the look of the "bias"
Solution: close out the front dart and transfer it to the neckline where it will eventually be covered by the collar.
Challenge: which grain to cut the collar? With the neckline dart, the laid on collar will never be able to match the fabric of the body. It can only match up to the dart, the worry is that it will just look like a mistake.
Solution: cut the collar/lapel so it is a contrast grain so the windowpane contrasts with the body- make a detail out of it.
Challenge: applying the fusible to the wool, making sure the right and left fronts are mirror images. dealing with shrinkage that comes with fusing.
Solution: Use a fusible that is somewhat translucent so I can see the windowpanes through it.
Draw out the pattern pieces on the fusible giving a clear CF line.
Block out the fabric in a single layer at the ironing table using a metre stick and a square, so the windowpanes stay square and true.
Chalk the pattern pieces onto the wool. including a clear CF placement line.
Apply the fusible to the wool carefully maintaining the alignment of CFs and overall placement.
Fuse one front, re block wool, chalk other front, and repeat making sure the alignment of the other front is a mirror image of the first.
At this point, the pieces are rough cut and I have to take them back to the table and check and redraw the pattern, because fusing always shrinks slightly.
Do the same process for the lapel/collar pieces.
Repeat for the second vest which must match the first.
This is the idea, partially done and placed roughly in position. We are going to put the welt pockets on the straight grain to match the lapels.
I think it will look very striking once it is finished, but oh boy it took a lot of time to get them cut out!
Monday, November 7, 2016
Dear dear Desmond
I first met Desmond Heeley in 1986. I was a new stitcher, and I was in my third professional job contract, working at The National Ballet of Canada on his production of the Merry Widow.
I was gathering strips of different colour fabrics for the underskirts of the Can Can dancers. Miles of them, tying off the gathering thread on the door knob of the wardrobe workroom and standing at the other end of the long hallway, pulling, ruching.
Anyway, one evening after my cutter and I had worked some overtime, we exited the building at the same time as Desmond, and him, desiring some company, gathered the both of us up and took us to dinner next door at a very expensive restaurant. I sat there completely out of my element, enthralled and quite speechless at finding myself in this position.
I realized yesterday at his memorial that he was the age I am now when we first met -isn't that funny- and I had no idea at that time that he would have a great influence on my future development as a cutter and that I would have the very great fortune of knowing him just a little.
There have been so many people that he worked with in the early days and became his "family" and so many stories told by him, told about him, stories of the development of theatre in this country, the crazy things they did for the love of their craft and of each other. I wish, and not for the first time in my life, that I had been born a little earlier, to have been able to know some people a bit more fully.
He gathered people to him, and he treated you as if you were the most important person in the world to him, his letters were the most vividly described, his interest and emotion so genuine.
I discovered quite by accident his mentor, Oliver Messel, when I read an article in an architectural magazine about homes built on the island of Mustique by a man who had been a theatre designer- and the accompanying images made me think of Desmond. When I asked him about it he told me that Messel was indeed his mentor, and later sent me, in a letter, a photocopy of a design of a spray of roses by Rex Whistler for the ballet Spectre of the Roses (Sadlers Wells) - just before WWII- great hero of mine, killed on the last day. a postscript to check him out online and another notation * He, Tanya & Oliver Messel my idols.
We shared a a love of Gilbert and Sullivan and Desmond sent me a few things over the years- a little book he found, a postcard, but by far the most amazing and generous was a sketch he made of the Fairy Queen in Iolanthe for the G&S society in New York and I am going to transcribe the exuberant handwritten note that came with it.
p.s. Am not quite sure that this is the sort of sketch one hangs BUT I thought it might make you smile- (and help G&S along) -
In the '60's I designed Iolanthe for Sadlers Wells opera- the first production away from the copyright (much concern from the diehards!) and a few sniffy folks at the Opera who thought that G&S was beneath them.
it was a huge success---this costume for the Fairy Queen was for a lady- named Heather Beggs- almost six feet tall--glorious voice & great style--at the end of the piece, "Up in the air sky high--" we actually flew her in a chariot made of Giant roses & pulled by two vast butterflies!---- two baby paniers spangled crin overskirt, (silver & gold brocade under!)-- the "ermine" was swansdown with black coque feathers----and the centre panel "chunky" leaves, roses, with a gauze layer on top!----
This sketch is a recreation done for the G&S Society here in NY
signed with a heart with an arrow through it,
Des
I was gathering strips of different colour fabrics for the underskirts of the Can Can dancers. Miles of them, tying off the gathering thread on the door knob of the wardrobe workroom and standing at the other end of the long hallway, pulling, ruching.
Anyway, one evening after my cutter and I had worked some overtime, we exited the building at the same time as Desmond, and him, desiring some company, gathered the both of us up and took us to dinner next door at a very expensive restaurant. I sat there completely out of my element, enthralled and quite speechless at finding myself in this position.
I realized yesterday at his memorial that he was the age I am now when we first met -isn't that funny- and I had no idea at that time that he would have a great influence on my future development as a cutter and that I would have the very great fortune of knowing him just a little.
There have been so many people that he worked with in the early days and became his "family" and so many stories told by him, told about him, stories of the development of theatre in this country, the crazy things they did for the love of their craft and of each other. I wish, and not for the first time in my life, that I had been born a little earlier, to have been able to know some people a bit more fully.
He gathered people to him, and he treated you as if you were the most important person in the world to him, his letters were the most vividly described, his interest and emotion so genuine.
I discovered quite by accident his mentor, Oliver Messel, when I read an article in an architectural magazine about homes built on the island of Mustique by a man who had been a theatre designer- and the accompanying images made me think of Desmond. When I asked him about it he told me that Messel was indeed his mentor, and later sent me, in a letter, a photocopy of a design of a spray of roses by Rex Whistler for the ballet Spectre of the Roses (Sadlers Wells) - just before WWII- great hero of mine, killed on the last day. a postscript to check him out online and another notation * He, Tanya & Oliver Messel my idols.
We shared a a love of Gilbert and Sullivan and Desmond sent me a few things over the years- a little book he found, a postcard, but by far the most amazing and generous was a sketch he made of the Fairy Queen in Iolanthe for the G&S society in New York and I am going to transcribe the exuberant handwritten note that came with it.
p.s. Am not quite sure that this is the sort of sketch one hangs BUT I thought it might make you smile- (and help G&S along) -
In the '60's I designed Iolanthe for Sadlers Wells opera- the first production away from the copyright (much concern from the diehards!) and a few sniffy folks at the Opera who thought that G&S was beneath them.
it was a huge success---this costume for the Fairy Queen was for a lady- named Heather Beggs- almost six feet tall--glorious voice & great style--at the end of the piece, "Up in the air sky high--" we actually flew her in a chariot made of Giant roses & pulled by two vast butterflies!---- two baby paniers spangled crin overskirt, (silver & gold brocade under!)-- the "ermine" was swansdown with black coque feathers----and the centre panel "chunky" leaves, roses, with a gauze layer on top!----
This sketch is a recreation done for the G&S Society here in NY
signed with a heart with an arrow through it,
Des
Thursday, November 3, 2016
mid 1950's references
I posted photos of the mid 1950's jackets that I recently made, and I thought it might be interesting to show some of the references I used to make my patterns.
There were the sketches and visual reference provided by the designer, but I like to research a bit more in order to make the patterns. I like to look at various drafts of the period I am trying to recreate but I don't actually use them because I don't have time to find out if they do or don't work on someone else's dime. I use my basic drafting set up and modify from there for fit and style.
I have a small collection of reference materials to use, and here are a few things that helped me.
I have had some opportunity to make 1950's suits before but I think I really was not successful in getting the silhouette right. I was determined to do better this time.
One thing I found was a chart showing proportionate back widths for jackets- you can see they offered three distinct widths for each chest size, depending on the style of jacket the customer wanted-
1. regular
2. modified drape or wide shouldered young men's
3. drape coats or lounge coats
You can see that for a size 38 the back width could be between 8 1/8 inches and 8 3/4 inches
Compare that to the standard proportion of approx 7 1/2 inches for a size 38 across back.
We wanted a more extremely young men's shape for these jackets and in looking at some of the period photos of these musicians, and other people of the period, the jackets were quite roomy, boxy and slightly oversized, and long. The waist shaping was minimal, the visual waistline was lower than the natural waist and the hip was quite slim. The shoulders were wide and quite square, buttoning point was lower, hence longer lapels, and pocket placement was lower as well.
These pages give an indication of the body silhouette, shoulder width, waist shaping, and overall jacket length.
These jackets were for young men so you can see that the studio style is longer, has lower set pockets and less waist shaping.
The length for someone 5'10" is 32".
Suit drafting uses a formula to determine length and a basic jacket length calculation is half height minus something- minus 4 inches or 1/2 h minus 1/16 of height.
If the actor is 5'10" (70") /2 = 35 minus 4= 31 inches
in metric which I prefer to use
178cm/2 = 89 minus 11.125cm = 78cm (30 3/4")
So these jackets are longer than that.
for 5'10" 70/2 = 35 inches so 35 -3 would give us a 32" length.
for 6'2" 74/2 =37 inches so 37-3 = 34 length
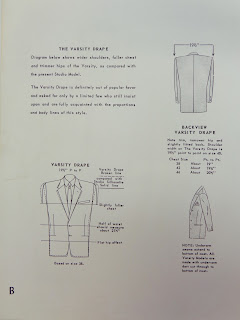
I started then with this information in hand, set up my drafting as I usually do, and made modifications until I though I had a good idea of where I was going.
I then cut out a half jacket in some cotton I had and put it on my stand. I photographed that and sent it to the designer for his input.
Once that was done, I took an idea from my colleague Evan and I drafted in half scale to show the changes and modifications to my basic draft. This is what I then referenced in making the subsequent drafts for the other jackets.
That half scale draft is now tucked away in my files for future reference.
There were the sketches and visual reference provided by the designer, but I like to research a bit more in order to make the patterns. I like to look at various drafts of the period I am trying to recreate but I don't actually use them because I don't have time to find out if they do or don't work on someone else's dime. I use my basic drafting set up and modify from there for fit and style.
I have a small collection of reference materials to use, and here are a few things that helped me.
I have had some opportunity to make 1950's suits before but I think I really was not successful in getting the silhouette right. I was determined to do better this time.
One thing I found was a chart showing proportionate back widths for jackets- you can see they offered three distinct widths for each chest size, depending on the style of jacket the customer wanted-
1. regular
2. modified drape or wide shouldered young men's
3. drape coats or lounge coats
You can see that for a size 38 the back width could be between 8 1/8 inches and 8 3/4 inches
Compare that to the standard proportion of approx 7 1/2 inches for a size 38 across back.
We wanted a more extremely young men's shape for these jackets and in looking at some of the period photos of these musicians, and other people of the period, the jackets were quite roomy, boxy and slightly oversized, and long. The waist shaping was minimal, the visual waistline was lower than the natural waist and the hip was quite slim. The shoulders were wide and quite square, buttoning point was lower, hence longer lapels, and pocket placement was lower as well.
These pages give an indication of the body silhouette, shoulder width, waist shaping, and overall jacket length.
These jackets were for young men so you can see that the studio style is longer, has lower set pockets and less waist shaping.
The length for someone 5'10" is 32".
Suit drafting uses a formula to determine length and a basic jacket length calculation is half height minus something- minus 4 inches or 1/2 h minus 1/16 of height.
If the actor is 5'10" (70") /2 = 35 minus 4= 31 inches
in metric which I prefer to use
178cm/2 = 89 minus 11.125cm = 78cm (30 3/4")
So these jackets are longer than that.
for 5'10" 70/2 = 35 inches so 35 -3 would give us a 32" length.
for 6'2" 74/2 =37 inches so 37-3 = 34 length
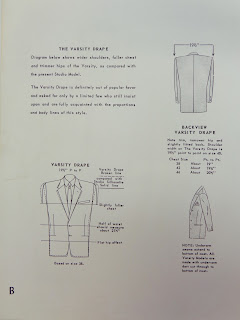
I started then with this information in hand, set up my drafting as I usually do, and made modifications until I though I had a good idea of where I was going.
I then cut out a half jacket in some cotton I had and put it on my stand. I photographed that and sent it to the designer for his input.
Once that was done, I took an idea from my colleague Evan and I drafted in half scale to show the changes and modifications to my basic draft. This is what I then referenced in making the subsequent drafts for the other jackets.
That half scale draft is now tucked away in my files for future reference.
Labels:
1950's,
20th century,
reference,
suit jacket,
tailoring
Sunday, October 30, 2016
losses and carrying on
Six months since I last posted.,
2016 has turned out to be so very trying, in so many ways and I am hoping it will come around and settle down a bit. This I wrote a few of months ago, and it still hasn't settled down. Now I am looking for the end of the year to close this chapter.
I/We have lost so many people, friends, colleagues, mentors, individuals who have connected the past of our profession to the present and future that it seems overwhelming.
I started to list them and I had to stop.
Carrying on is what we have to do and in that spirit we continue on.
The studio is up and functioning, and I am hoping that the scent of scented candles will eventually go away in time. (this sentence brought to you from the department of redundancy department)
I am putting my hopes in time and Febreze unscented. It has been an enjoyable space to work in so far. The cats from the other space have been brought over and they are doing their job, keeping those pesky mice at bay. Jay's kiln is wired in and he is producing his beautiful work again. Andy and Rob are still organizing the wood and machinery and before getting back into the swing of things making cutting boards and such, they are building some very nice feral cat winter shelters.
I finished a project for a client that I felt was a bit of an experiment, making a suit long distance and doing the fitting over Skype. I am happy to say that it worked out quite well which is a relief for me. Here is the jacket in process. Silvia did a fabulous job with it, and I made the trousers and waistcoat.
The first studio project though was something sparkly, four jackets for Million Dollar Quartet. I usually do projects that allow for me to fit the actors but this time it was long distance and we did it with measurements and photos and a couple of cross your fingers and hope it all works out. Which they did, so a win win for all of us. Design: Cory Sincennes for the Citadel Theatre, Edmonton Alberta
Poor Elvis, I don't think I got a finished shot of that jacket. :(
I have a few more projects coming up and some pictures of some work that happened over the past six months. I also want to give some thought and discussion about training new tailor/cutters which is a topic that will be very pertinent in the near future.
2016 has turned out to be so very trying, in so many ways and I am hoping it will come around and settle down a bit. This I wrote a few of months ago, and it still hasn't settled down. Now I am looking for the end of the year to close this chapter.
I/We have lost so many people, friends, colleagues, mentors, individuals who have connected the past of our profession to the present and future that it seems overwhelming.
I started to list them and I had to stop.
Carrying on is what we have to do and in that spirit we continue on.
The studio is up and functioning, and I am hoping that the scent of scented candles will eventually go away in time. (this sentence brought to you from the department of redundancy department)
I am putting my hopes in time and Febreze unscented. It has been an enjoyable space to work in so far. The cats from the other space have been brought over and they are doing their job, keeping those pesky mice at bay. Jay's kiln is wired in and he is producing his beautiful work again. Andy and Rob are still organizing the wood and machinery and before getting back into the swing of things making cutting boards and such, they are building some very nice feral cat winter shelters.
I finished a project for a client that I felt was a bit of an experiment, making a suit long distance and doing the fitting over Skype. I am happy to say that it worked out quite well which is a relief for me. Here is the jacket in process. Silvia did a fabulous job with it, and I made the trousers and waistcoat.
The first studio project though was something sparkly, four jackets for Million Dollar Quartet. I usually do projects that allow for me to fit the actors but this time it was long distance and we did it with measurements and photos and a couple of cross your fingers and hope it all works out. Which they did, so a win win for all of us. Design: Cory Sincennes for the Citadel Theatre, Edmonton Alberta
Poor Elvis, I don't think I got a finished shot of that jacket. :(
I have a few more projects coming up and some pictures of some work that happened over the past six months. I also want to give some thought and discussion about training new tailor/cutters which is a topic that will be very pertinent in the near future.
Sunday, May 1, 2016
checking things off the list
Today I got to check one big thing off my list!
The studio has been moved. Ten adults, two kids, two truckloads and 4 and a half hours later, done. Thanks to all my friends who helped. Terry for providing a truck and Jeff who fixed the hydraulic lift switch at the new place, so unloading was a breeze. The kids had what is likely a fairly rare opportunity to ride up and down on a very old freight elevator- the ones with the pull down wooden gates and the kind where the operator (me) has to manually stop so the floor levels are even.
Of course the new space is not set up, and we need to do some work on it first, so everything is stacked and under wraps for now.
But one thing is off the list.
Now we can pack up the car with our daughter's belongings and move her tomorrow. I am missing a day of work but there are only so many things you can do on one week end.
I had a tech dress yesterday until 7pm and thankfully they got through a very technically demanding show. That is one more thing to check off my list as well.
I don't often list my workload here in full, but all of this list making makes me think I should let you in on how much work we have produced since mid January. This is me pattern making and with four tailors plus one extra set of hands for three weeks.
so here goes
Show 1: 1940's plus fantasy costumes- (all this built from scratch)
9 jackets
6 waistcoats
5 trousers
1 pair pleated shorts
5 long sleeved shirts
3 unitards
2 medieval gowns
2 velvet capes
2 fur capelets
1 wolf in fake fur including a tail and all supports structure
2 centaur costumes
1 bodice for a tree
1 pair of trousers for a tree (stilt walker)
1 lion cape
1 lion cowl
2 sets of leather spats with fake fur trim
2 sets of protective gear for wearing a prop
1 cowl and hood
a variety of stock costumes including 3 trousers made into shorts, 4 wraiths, a witch's footman, shirts collars, and more that I cannot think of right now.
Show 2: 1940's (all this built from scratch)
2 three piece suits
2 shirts
1 two piece suit
2 pair trousers
altering a variety of stock jeans t shirts and puchased clothing
We are already behind for the next show, so I am not sure how much spare time I will have in the next little while to post but we will see.
How often do you get to make a tree? A theatrical tailor's life is quite varied for sure!
Kudos to Heather in props who really made him into a tree. Great work!
The studio has been moved. Ten adults, two kids, two truckloads and 4 and a half hours later, done. Thanks to all my friends who helped. Terry for providing a truck and Jeff who fixed the hydraulic lift switch at the new place, so unloading was a breeze. The kids had what is likely a fairly rare opportunity to ride up and down on a very old freight elevator- the ones with the pull down wooden gates and the kind where the operator (me) has to manually stop so the floor levels are even.
Of course the new space is not set up, and we need to do some work on it first, so everything is stacked and under wraps for now.
But one thing is off the list.
Now we can pack up the car with our daughter's belongings and move her tomorrow. I am missing a day of work but there are only so many things you can do on one week end.
I had a tech dress yesterday until 7pm and thankfully they got through a very technically demanding show. That is one more thing to check off my list as well.
I don't often list my workload here in full, but all of this list making makes me think I should let you in on how much work we have produced since mid January. This is me pattern making and with four tailors plus one extra set of hands for three weeks.
so here goes
Show 1: 1940's plus fantasy costumes- (all this built from scratch)
9 jackets
6 waistcoats
5 trousers
1 pair pleated shorts
5 long sleeved shirts
3 unitards
2 medieval gowns
2 velvet capes
2 fur capelets
1 wolf in fake fur including a tail and all supports structure
2 centaur costumes
1 bodice for a tree
1 pair of trousers for a tree (stilt walker)
1 lion cape
1 lion cowl
2 sets of leather spats with fake fur trim
2 sets of protective gear for wearing a prop
1 cowl and hood
a variety of stock costumes including 3 trousers made into shorts, 4 wraiths, a witch's footman, shirts collars, and more that I cannot think of right now.
Show 2: 1940's (all this built from scratch)
2 three piece suits
2 shirts
1 two piece suit
2 pair trousers
altering a variety of stock jeans t shirts and puchased clothing
We are already behind for the next show, so I am not sure how much spare time I will have in the next little while to post but we will see.
How often do you get to make a tree? A theatrical tailor's life is quite varied for sure!
Kudos to Heather in props who really made him into a tree. Great work!
Sunday, April 10, 2016
a man in wolf's clothing?
It has been quite hectic here with all that is going on. I think I say this a lot don't I?
I mentioned in a reply to a comment that everything is happening April 30th!
We need to assist our daughter to move out of her university digs and into a sublet in the city she is in, and I have a tech dress rehearsal on the 30th too. I guess my studio is moving on May 1st, and therefore my dear husband is on his own for the big city/daughter move. Whew!
I believe that I have been able to secure a new spot for my studio -knock on wood- but I am waiting for confirmation and a few more small details to be worked out. It is a relief, and just in time because I have more than enough stress with work and life in general.
I still need to hire a truck and finish packing up in preparation. I will also need to do some painting and flooring work before I can set things up, so I don't think I will be set up and functioning right away. Oh well, at least there is a light on the horizon.
So I actually have two shows going into tech in three weeks, one on the 28th and the other on the 30th. Then I have a small window to get a show together for the mid May period. The pace is not going to get slower for a while yet.
Here's one of two costumes that I fit yesterday, which I am quite happy with. This is an example of what I term "there is no formula" for doing the work we do. Trial and error experience and adaptation. Or flying by the seat of your pants way of working!
This is the wolf.
This has been in limbo for a few weeks while we were backed up with other priorities. The tail was ready though! There was a lot of pattern making to do for this costume.
The base layer to this costume is a stretch legging and a long sleeved stretch top that zips up the front.
I think it should have been a unitard and it may still get joined together but for now it is two pieces.
Pattern number one and two- actually, I had to redo the patterns as I was given a fabric to use that had a different stretch factor, but there wasn't enough of it in the end to make the whole costume. So ditch those patterns, get new fabric, recalculate the stretch and make new patterns!
We also needed a pattern for the basque that supports the tail. That pattern I developed from a skirt draft. ( I am not actually following a specific draft, merely the concept of it here).
The next set of pattern making involved the fur layer.
The fur does not stretch. We have a few hanging stands in the wardrobe, but the one with a good size for the torso has legs only to above the knee, and the stands with full legs have short stocky bodies. I decided to trust my flat pattern making skills to figure it out rather than draping something on a stand.
I then needed to draft for the fur layer and figure out how it could be manipulated to fit closely in the body and allow the actor full movement. He demonstrated some of the fight choreography (full lunges in armour) in the first fitting, so that informed my subsequent thinking.
The fur on the wolf's tail was applied in sections to allow movement, and I applied the same principle to the leg area.
I drafted up a trouser pattern outline, and then modified it to be closer fitting, then I figured out the areas of overlap.
My actual pattern is so marked up with thinking lines that I drew a little diagram of what I did.
I didn't need to cover the areas of the body that are covered with armour, such as the lower legs which have greaves, and a knee piece - what are they called? Poleyns, I believe.
The thigh area fur is cut in four pieces. It is seamed up the back of the leg and shaped to follow the contours of the thigh and buttocks. It has an inseam and outseam, and a seam up the front of the leg where I left adjustment room- extra seam allowance.
The over layer is like a pair of short shorts.
I reduced the girth a bit as I am working off a trouser draft, which is too roomy in general. I also darted out from the CF and CB lines to the hem of the shorts in order to get a closer fit there.
The basque was made of duck and corseting and is heavily boned with spiral steels in order to support the escutcheon for the tail.
We found out that we need to shorten the spring inside the tail as you can see! Move the escutcheon piece upwards as well.
The escutcheon piece has holes drilled in it so it can be sewn on. It needs to have some kind of keeper as well, because the tail is very bouncy and popped out of the holder. Well that is what the fittings are for- figuring stuff out- what works and what doesn't.
We will then cover the basque with fur.
In the course of talking this through with Susy- who put it all together, we found that we could sew an elastic to the edge of the fur, and use that elastic as a means to attach the fur to the leggings. That means the thigh piece can be a little bigger than the thigh measurement, we can ease the fur to the elastic, and when it is attached there is still some give for muscle expansion.
The same principle with the shorts- the lowered waist can be eased onto elastic then attached to the stretch legging. This leaves the fur shorts free to move independently from the fur on the thigh. and also still be a pull on garment.
I had a lucky guess in how nicely the pieces worked together. The fur is bulky so the over layer needs to be bigger than you might think, and all our layers worked well together. you couldn't tell they were actually two pieces.
We did a similar process with the chest and armhole and sleeves. The fur elbow to upper bicep in one piece, the fur upper sleeve attached to the fur armhole facings/chest area, but left loose over the upper arm piece.
We will leave the armholes and sleeve of the stretch and fur separate so the fur pieces just float over the stretch. That should allow the most freedom of movement- I hope it does anyway. Seemed good on the day anyway.
The other fitting was for a suit- which I guess i will talk about later as this post has gone on and taken me most of the day to get together.
Later....
also
Goodbye to our friend, Paul "eggs" Benedict, sound engineer extraordinaire, and all around lovely person.
2016 has been difficult- losing so many people we have had in our lives.
I mentioned in a reply to a comment that everything is happening April 30th!
We need to assist our daughter to move out of her university digs and into a sublet in the city she is in, and I have a tech dress rehearsal on the 30th too. I guess my studio is moving on May 1st, and therefore my dear husband is on his own for the big city/daughter move. Whew!
I believe that I have been able to secure a new spot for my studio -knock on wood- but I am waiting for confirmation and a few more small details to be worked out. It is a relief, and just in time because I have more than enough stress with work and life in general.
I still need to hire a truck and finish packing up in preparation. I will also need to do some painting and flooring work before I can set things up, so I don't think I will be set up and functioning right away. Oh well, at least there is a light on the horizon.
So I actually have two shows going into tech in three weeks, one on the 28th and the other on the 30th. Then I have a small window to get a show together for the mid May period. The pace is not going to get slower for a while yet.
Here's one of two costumes that I fit yesterday, which I am quite happy with. This is an example of what I term "there is no formula" for doing the work we do. Trial and error experience and adaptation. Or flying by the seat of your pants way of working!
This is the wolf.
This has been in limbo for a few weeks while we were backed up with other priorities. The tail was ready though! There was a lot of pattern making to do for this costume.
The base layer to this costume is a stretch legging and a long sleeved stretch top that zips up the front.
I think it should have been a unitard and it may still get joined together but for now it is two pieces.
Pattern number one and two- actually, I had to redo the patterns as I was given a fabric to use that had a different stretch factor, but there wasn't enough of it in the end to make the whole costume. So ditch those patterns, get new fabric, recalculate the stretch and make new patterns!
We also needed a pattern for the basque that supports the tail. That pattern I developed from a skirt draft. ( I am not actually following a specific draft, merely the concept of it here).
The next set of pattern making involved the fur layer.
The fur does not stretch. We have a few hanging stands in the wardrobe, but the one with a good size for the torso has legs only to above the knee, and the stands with full legs have short stocky bodies. I decided to trust my flat pattern making skills to figure it out rather than draping something on a stand.
I then needed to draft for the fur layer and figure out how it could be manipulated to fit closely in the body and allow the actor full movement. He demonstrated some of the fight choreography (full lunges in armour) in the first fitting, so that informed my subsequent thinking.
The fur on the wolf's tail was applied in sections to allow movement, and I applied the same principle to the leg area.
I drafted up a trouser pattern outline, and then modified it to be closer fitting, then I figured out the areas of overlap.
My actual pattern is so marked up with thinking lines that I drew a little diagram of what I did.
I didn't need to cover the areas of the body that are covered with armour, such as the lower legs which have greaves, and a knee piece - what are they called? Poleyns, I believe.
The thigh area fur is cut in four pieces. It is seamed up the back of the leg and shaped to follow the contours of the thigh and buttocks. It has an inseam and outseam, and a seam up the front of the leg where I left adjustment room- extra seam allowance.
The over layer is like a pair of short shorts.
I reduced the girth a bit as I am working off a trouser draft, which is too roomy in general. I also darted out from the CF and CB lines to the hem of the shorts in order to get a closer fit there.
The basque was made of duck and corseting and is heavily boned with spiral steels in order to support the escutcheon for the tail.
We found out that we need to shorten the spring inside the tail as you can see! Move the escutcheon piece upwards as well.
The escutcheon piece has holes drilled in it so it can be sewn on. It needs to have some kind of keeper as well, because the tail is very bouncy and popped out of the holder. Well that is what the fittings are for- figuring stuff out- what works and what doesn't.
We will then cover the basque with fur.
In the course of talking this through with Susy- who put it all together, we found that we could sew an elastic to the edge of the fur, and use that elastic as a means to attach the fur to the leggings. That means the thigh piece can be a little bigger than the thigh measurement, we can ease the fur to the elastic, and when it is attached there is still some give for muscle expansion.
The same principle with the shorts- the lowered waist can be eased onto elastic then attached to the stretch legging. This leaves the fur shorts free to move independently from the fur on the thigh. and also still be a pull on garment.
I had a lucky guess in how nicely the pieces worked together. The fur is bulky so the over layer needs to be bigger than you might think, and all our layers worked well together. you couldn't tell they were actually two pieces.
We did a similar process with the chest and armhole and sleeves. The fur elbow to upper bicep in one piece, the fur upper sleeve attached to the fur armhole facings/chest area, but left loose over the upper arm piece.
We will leave the armholes and sleeve of the stretch and fur separate so the fur pieces just float over the stretch. That should allow the most freedom of movement- I hope it does anyway. Seemed good on the day anyway.
The other fitting was for a suit- which I guess i will talk about later as this post has gone on and taken me most of the day to get together.
Later....
also
Goodbye to our friend, Paul "eggs" Benedict, sound engineer extraordinaire, and all around lovely person.
2016 has been difficult- losing so many people we have had in our lives.
Labels:
21st century,
fittings,
pattern drafting,
random,
stretch,
techniques,
workload
Saturday, March 19, 2016
Carry on!
I thought that I should follow up on the thoughts about structure. This won't be that post as I am finding myself with no spare time these days.
I have been trying to get photos of this dress and all its underpinnings, and I keep missing the time when it is on the dress form in its most basic form, but I will get them!
My colleague Carol, is making three dresses in this style- talk about needing underpinnings to support a shape- I think it is one of the most extreme shapes of women's fashion don't you?
Here's a link to the V&A museum which describes a dress of this type they have in their collection.
For my part, last week, among other things, I made a pair of trousers for a tree.
Yes. I am still working out the structure to support the form, and the actor, designer, and choreographers and coaches are working out whether the stilts will be set at a maximum of 48 inches from the ground or whether that is too tall!
It made me a bit nervous at the fitting watching the actor work at 28 inches up so I cannot imagine walking around four feet off the ground. We will see.
I have not had any luck so far finding another studio space but I am trying to be hopeful but also to plan for the possibility of putting my equipment in storage for a time.
There just are not enough hours in the day or week to work 40 hours, eat sleep and track down landlords and property owners and set up times to view locations.
Anyway, carry on! as they say.
I have been trying to get photos of this dress and all its underpinnings, and I keep missing the time when it is on the dress form in its most basic form, but I will get them!
My colleague Carol, is making three dresses in this style- talk about needing underpinnings to support a shape- I think it is one of the most extreme shapes of women's fashion don't you?
Here's a link to the V&A museum which describes a dress of this type they have in their collection.
For my part, last week, among other things, I made a pair of trousers for a tree.
Yes. I am still working out the structure to support the form, and the actor, designer, and choreographers and coaches are working out whether the stilts will be set at a maximum of 48 inches from the ground or whether that is too tall!
It made me a bit nervous at the fitting watching the actor work at 28 inches up so I cannot imagine walking around four feet off the ground. We will see.
I have not had any luck so far finding another studio space but I am trying to be hopeful but also to plan for the possibility of putting my equipment in storage for a time.
There just are not enough hours in the day or week to work 40 hours, eat sleep and track down landlords and property owners and set up times to view locations.
Anyway, carry on! as they say.
Friday, March 4, 2016
Such a week!
All my plans kind of went out the window this week.
I woke up Monday after a great week end, with this strange heaviness over me. I was walking to work and wondering why I was feeling that way. "Carry on!" as they say, but at 9:30 am I received a phone call from the building manager where I have my personal studio/workspace.
"This cannot be good" I thought, and it wasn't. The factory where I am situated is evicting all its tenants because they need the space.
We have quite a history in the furniture business here.
It is an old furniture factory, built in 1900 and 25 years ago the building had a lot of unused space and they started leasing space to artisans who were grateful to have a reasonably priced place to create. There have been woodworkers, potters, cobblers, artists and yes tailors and cutters all clustered on a floor or two there.
Recently the business has been storing a lot of product there as the storage of wood products was grandfathered into the system, and they need their space back.
There is a potter and woodworker whose livelihoods are made by what they produce there. Myself and my colleagues - another cutter and a theatrical milliner and a wig maker are slightly better off in that we work part of the year for a large theatre and use our space to generate income for the time we are "unemployed" laid off. We can rent at the theatre but it is not guaranteed to be available when we need it and for some of us, our freelance projects overlap slightly with our "employment" and the rentals stop once the theatre staff start work. Which is totally reasonable.
Our situation is complicated because we had reasonable rents which meant we could absorb the rental costs into a partial year of earning potential, but these days, it is so difficult to find light industrial space at all, let alone at a reasonable rate. I see so many places that are empty (sometimes for years) but the landlords would rather they stay that way rather than reducing the rent and having a tenant.
There must be some advantage to them doing so I just don't understand it.
So we have to go. Where? I don't know, but the search is on and it is proving difficult so far.
We have banded together to look for another location and I guess I will have to put some extra projects on hold while I try to work this out.
So, that is my tale of woe.
p.s. a Facebook page has been set up for those of us who were members of the Cutter and Tailor forum, please visit it and lets keep in touch. I hope to see you there. If the link doesn't work check the comment section two posts back.
I woke up Monday after a great week end, with this strange heaviness over me. I was walking to work and wondering why I was feeling that way. "Carry on!" as they say, but at 9:30 am I received a phone call from the building manager where I have my personal studio/workspace.
"This cannot be good" I thought, and it wasn't. The factory where I am situated is evicting all its tenants because they need the space.
We have quite a history in the furniture business here.
It is an old furniture factory, built in 1900 and 25 years ago the building had a lot of unused space and they started leasing space to artisans who were grateful to have a reasonably priced place to create. There have been woodworkers, potters, cobblers, artists and yes tailors and cutters all clustered on a floor or two there.
Recently the business has been storing a lot of product there as the storage of wood products was grandfathered into the system, and they need their space back.
There is a potter and woodworker whose livelihoods are made by what they produce there. Myself and my colleagues - another cutter and a theatrical milliner and a wig maker are slightly better off in that we work part of the year for a large theatre and use our space to generate income for the time we are "unemployed" laid off. We can rent at the theatre but it is not guaranteed to be available when we need it and for some of us, our freelance projects overlap slightly with our "employment" and the rentals stop once the theatre staff start work. Which is totally reasonable.
Our situation is complicated because we had reasonable rents which meant we could absorb the rental costs into a partial year of earning potential, but these days, it is so difficult to find light industrial space at all, let alone at a reasonable rate. I see so many places that are empty (sometimes for years) but the landlords would rather they stay that way rather than reducing the rent and having a tenant.
There must be some advantage to them doing so I just don't understand it.
So we have to go. Where? I don't know, but the search is on and it is proving difficult so far.
We have banded together to look for another location and I guess I will have to put some extra projects on hold while I try to work this out.
So, that is my tale of woe.
p.s. a Facebook page has been set up for those of us who were members of the Cutter and Tailor forum, please visit it and lets keep in touch. I hope to see you there. If the link doesn't work check the comment section two posts back.
I am off for my annual ski week end (no wifi) and will come back refreshed and energized, ready to take on the real estate world!
Sunday, February 28, 2016
Tail tales
So here we are further along in the process of making the wolf's tail.
The props department has provided us with a way of attaching the tail to the body. The tail gets this metal button end that screwed into the spring.
This then will slot into a metal plate that looks just like a large escutcheon/ key hole. The metal plate has holes drilled into it so we can sew it to the basque. When we get to that point, I will take some photos of it.
Before we get to that point we started to cover the tail with the fake fur.
Beginning at the end of the tail, I cut a piece to try out. The darts are cut on the lines and zigged together, then we tried it on the form, made some adjustments, and sewed it to the net fabric at the first segment.
The trick with cutting fake fur is to not cut the fur, just the backing fabric. I often use an exacto blade, or use just the tips of a very sharp pair of scissors. Wear a mask while cutting and sewing and have a sticky roller nearby so you can go home not covered in fibres!
Even with careful handling, the fibres get everywhere, just the same as glitter does!
There is a separate piece of fake fur cut for each segment, to allow the segments to bend.
Each of these pieces overlaps the previous one, and needs to be loose enough to allow movement.
You cannot predetermine the segment sizes as overlapping the fake fur adds quite a lot of bulk. After conferring about the process, Silvia happily took on the task of figuring out the best size for each segment, and attaching them to the base.
The loose edges of each section are cut with jagged edges so there is a not a defined line between them.
Here you can see we have added a darker covering fabric close to the base of the tail where a lot of the bend will happen. If there was ever a glimpse underneath one of those layers, you will not see the white or pink of the structure.
We covered the tail up to the button, and are now waiting for a fitting of the costume base and the basque.
It is fun to have a chance to createsomething different every once in a while!
Saturday, February 27, 2016
Cutter and Tailor forum?
Hello,
As you can see in the comments recently, many of us are wondering what has happened with the Cutter and Tailor forum. It just stopped being accessible last week and attempting to access it results in an Internal Server error message.
Some of you with whom I have interacted with there have emailed me through the blog to ask if I knew anything about this.
I am sorry to say that I don't know what is going on. I have been unable to contact Sator - the owner of the forum. I have been in touch with one of the moderators, SG, and he seemed to be as surprised as we all have been about the sudden changes. He also does not have the means to contact Sator, so here we are.
I sincerely hope that the site has not been shut down intentionally. I would have liked the chance to help support its existence, if money for hosting was an issue. I found the information to be quite informative, and the knowledge within quite useful. I also enjoyed the connection with other like minded people pros and amateurs alike.
I know there were discussions recently amongst the professionals who did post, about what the purpose of the site was, and what it should be. I believe the purpose of the forum was to facilitate communication amongst professional tailors, but strangely, many professionals were members but never contributed.
I am not sure why that is, maybe people are too busy or too unwilling to share their processes, the field is quite guarded after all.
Many thought that too many amateurs were trying to access information and assistance with processes far beyond their knowledge or capabilities, and yes that did happen, but on the other hand, you cannot expect otherwise in a public forum.
Myself, I am at the point in my experience that I don't need stacks of information to do my job, but I like having it around. I like to see other ways of construction past and present and I enjoy learning.
The bigger concern in my mind, is for the up and coming people interested in the field. I know a lot of what was on the site is available if you google hard enough, but the site was an invaluable resource of accumulated materials all in one place.
I miss it.
I have contact with a few members from the site, and if I do hear any news I will post it here. Likewise if you know what is going on please let me know.
As you can see in the comments recently, many of us are wondering what has happened with the Cutter and Tailor forum. It just stopped being accessible last week and attempting to access it results in an Internal Server error message.
Some of you with whom I have interacted with there have emailed me through the blog to ask if I knew anything about this.
I am sorry to say that I don't know what is going on. I have been unable to contact Sator - the owner of the forum. I have been in touch with one of the moderators, SG, and he seemed to be as surprised as we all have been about the sudden changes. He also does not have the means to contact Sator, so here we are.
I sincerely hope that the site has not been shut down intentionally. I would have liked the chance to help support its existence, if money for hosting was an issue. I found the information to be quite informative, and the knowledge within quite useful. I also enjoyed the connection with other like minded people pros and amateurs alike.
I know there were discussions recently amongst the professionals who did post, about what the purpose of the site was, and what it should be. I believe the purpose of the forum was to facilitate communication amongst professional tailors, but strangely, many professionals were members but never contributed.
I am not sure why that is, maybe people are too busy or too unwilling to share their processes, the field is quite guarded after all.
Many thought that too many amateurs were trying to access information and assistance with processes far beyond their knowledge or capabilities, and yes that did happen, but on the other hand, you cannot expect otherwise in a public forum.
Myself, I am at the point in my experience that I don't need stacks of information to do my job, but I like having it around. I like to see other ways of construction past and present and I enjoy learning.
The bigger concern in my mind, is for the up and coming people interested in the field. I know a lot of what was on the site is available if you google hard enough, but the site was an invaluable resource of accumulated materials all in one place.
I miss it.
I have contact with a few members from the site, and if I do hear any news I will post it here. Likewise if you know what is going on please let me know.
Sunday, February 21, 2016
structure: pool noodles and springs
Okay, we are heading off into other territory here, definitely away from tailoring, although I do have some nice 1930's and '40"s suits to make this season. More about those later.
So what the heck is this on my table?
Any guesses?
Well it is going to be a wolf's tail. Yes indeed.
Many years ago I worked on a production of Wind in the Willows at The Grand Theatre.
If you know the story, it has animal characters and they are often charmingly portrayed as animals with human characteristics, wearing Lovely Edwardian clothing. It was a fabulous production, the actors included Douglas Campbell as Badger, and, well, if you know who he was then you can imagine his presence in that role.
The costuming was properly Edwardian and the characters had tails which emerged from their velvet breeches or wool trousers.
The tails were made by a very talented woman, Elaine Ball, and I was recently asking her about how she made them (as I could only remember snippets of something we did almost 20 years ago-wow).
Strangely enough, she was in the midst of teaching this very thing to a class of costumers.
She graciously shared some photos that jogged the old memory. I shared these with Kim my colleague who made the prototype as well as the structure above.
So, the tails are made of pool noodles, shaped and tapered a bit as you can see, and each pool noodle segment is separated by a large wooden bead.
The base of the tail uses a door spring, that feeds through the first few sections, as well as a heavy elastic shock cord which goes through to the end section.
We will construct a snug fitting basque for the actor to wear, and it will have an attachment plate at the back for the tail. The tail here still needs an attachment at the end of the spring-but the spring allows the tail to sit flush against the basque and hang quite naturally.
This tail has had a mesh fabric applied over the segments in preparation for covering it with fake fur.
I hope I will get to that task next week, cutting out fur sections as well as making the basque and getting the whole thing together, including another unitard that is worn with this. Oh and there's armour too.
I will also post about the suits as I have a couple of challenging figures to make for and they all need to look the same. Interesting challenges this season for sure.
Saturday, February 13, 2016
Radio silence has ended! plus cool stuff
Hello one and all,
I realized today that I have not had much to say on the blog recently.
I am trying to figure out why that is.
I do have a lot of thoughts, but the topics are either so complicated that I give up trying to write about them or so fleeting in nature that they don't prod me to write.
For the moment though, you may may be interested in the fact that as a tailor- cutter in a theatre, I am called on to make all sorts of garments, and this year I do have some suits, yes, but I have a bit more of things like this.
here's a little video link to a bit more of Kenny's work....please watch it, it gives me goosebumps.
I realized today that I have not had much to say on the blog recently.
I am trying to figure out why that is.
I do have a lot of thoughts, but the topics are either so complicated that I give up trying to write about them or so fleeting in nature that they don't prod me to write.
For the moment though, you may may be interested in the fact that as a tailor- cutter in a theatre, I am called on to make all sorts of garments, and this year I do have some suits, yes, but I have a bit more of things like this.
yes, unitards or variations on the theme!
I often joke with people as I am taking their measurements, that I need to take some certain specific ones, in case we have to make them a unitard! Sometimes that happens.
We actually don't take the detailed type of measurements that a place like cirque will take for their costumes, so when unitards or other stretch wear arises, it can be a bit of hit or miss.
These types of garments and the patterns required for them depend greatly on the fabric chosen.
Can I put a public service announcement here for all designers? Please, please, buy good all way stretch. Spend the money for it. Fabric that stretches in both directions makes for easier pattern making and for wearing.
In this case, I have basically a one way stretch fabric. I had to cut it with the stretch around the body and the non-stretch vertically. The upper body will not be seen, so I have worked around the lack of stretch in the crushed velvet legs by adding a very stretchy fabric above the waist. In this manner I hope to have given the actor some comfort in being able to sit down easily at least.
This was a first fit, all zigged together with somewhat incorrect (old) measurements, so I have some work to do, tweaking the pattern.
Oh, what is that thing he is attached to you ask?
It is a wire frame body of an animal. You will have to wait for a bit for more details, but it also is a first trial fit on the actor. Our prop maker Kenny (a mastermind of an artist, sculptor and maker of cool things) has built these frames for the show we are working on. The bands around the actor's thighs are attached to wires that connect to the back legs of the sculpture, so when the actor walks, the animal legs walk as well. Very cool.
Strange co-incidence, Kenny and I trained in the same fine arts program but he graduated just before I started. We have been working together for 25+ years and only found this out last month! We had the same instructors and had a moment reminiscing about that time. Isn't it funny how these things happen?
I think this season will feature structure quite prominently as I look around the wardrobe these days, so I will endeavour to get some postings up about that and rekindle my blogging spirit.
Cheers
Subscribe to:
Posts (Atom)