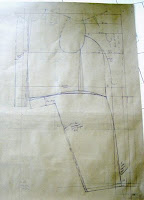
So here's the beginning of my pattern for the Footman's Coatee. Again, my apologies for the photo quality, I had to put these on the floor to take a full picture.
First the basic information:
Measurements- I didn't take the measurements for this actor and in fact I have never seen him, which makes me work on the side of caution. I think that some of the numbers are wrong and therefore when in doubt, I revert to standard calculations and hope for the best.
I read through, well actually I skimmed through the period draft looking for the details that will help recreating this look. I find some of these drafting instructions so tedious that my eyes glaze over while deciphering them.
As a side note, I find it interesting to look at my patterns like this, because I see right now things that I want to change....hmmm, anyway, onwards.......
One concern that I had right away is that these coats are supposed to be closed with a link fastening, but the draft is
fully double breasted. Mistake or something that I am missing? I decided that I would have to modify it because it didn't feel right.
I'll start with the back:
I decided to draft this without seam allowances because I feel its easier to develop the shape that way.
I start with a long vertical construction line and a line perpendicular to that at the top.
I find the scye line and it's divisions above that, square out.
Mark the width and height of the back neck and draw it in.
Mark the waist length. His waist length measurement seemed a bit long so I reverted to using 1/4 of height as his natural waist and drop 2" for the "fashion waist".
Mark the full length of the coat. I chose to start 4" above his nape to back of knee measurement
Mark in the amount of waist suppression at the CB waist.
Draw in a gently curved CB line.
Mark out the across back width and square up to the top line.
Mark out the shoulder slope and draw in a rough back shoulder line.
Mark in the width of the CB panel at the waist line, using the draft as a guide to the width.
Determine where the curved back seam from the draft falls on the scye line and where it ends at the back armhole, and draw it in.
I start with a 3cm suppression at the side back waist and draw in the other side of the curved back seam.
Measure along the scye line, 1/2 chest plus 5cm ease for the CF line and square up and down.
I use the scye line as one base for balance in the draft, so I measure the seam line of the curved back seam, on the back panel, from the scye line to the armhole. I then measure the corresponding seam line on the side back panel from the scye line to armhole and extend it as required so they are the same measurement. I go through the same procedure form the scye line down to the waist for these seams to reconcile the measurements.
Measure the width for the armhole, and make a mark.
Now I start working back from the centre front line.
I think his chest width measurement could be wrong so I have to use my judgement here. I mark it and decide on a happy medium between the armhole width and the cross front measurement. Square up to the top line. I measure toward the front along the top line 1/6 working scale on the square(neck width), and again 1/6 scale. I draw in a tentative front shoulder line.
Now I mark 2.5 cm below the drafted waist on the CF line and check the measurement I have for nape to CF waist against the pattern, and I raise the front balance on this pattern, 1 and 1/4 " above the top line and square up my neck and shoulder lines, redraw them in the new location. Then I draw in a basic armhole shape.
I then measure down from the neck point 1/6 working scale minus 2cm and give myself a guide line for the gorge line angle. Draw it in.
Now I need to decide about the link closure and how to make sense of the look of the seamed on DB lapel.
I will stop here and continue tomorrow.
Oh yeah, ok, I know I use metric and imperial measurements interchangeably, or some may say randomly, but I grew up with imperial and draft in metric and use whatever measurement system that suits the situation-no pun intended. You'll just have to forgive me.