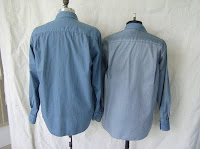
Here are two shirts from the same maker, put in the same dye pot at the same time. The shirt on the left is plain cotton, the other is "no-iron" cotton.
The buyer didn't realize that she grabbed the no- iron shirt and the dyer didn't notice it before the dye process began.
The no-iron shirt has been sprayed with a chemical after it is made. You can see that the areas where the spray didn't hit that dyed darker, and you can see some of the over spray drips.
It's shocking that people are wearing this chemical next to their skin. It's all to save a few minutes pressing your shirt but it could be shortening your life. Is the chemical used indicated anywhere on the labels- no it isn't. Would you buy this shirt if you knew what had been done to it to make your life easier?
No wonder people are getting sick more and more.
I'm disgusted by it.
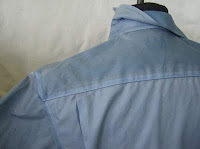
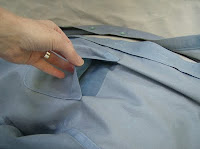
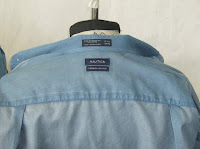