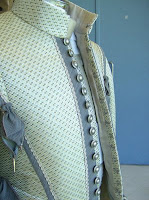
We used alternating hooks and eyes down the front. The buttons are decorative and are stitched just to the edge of the front so that when the hooks are done up, all you see is the illusion of the buttons being the closures.
If you put all the hooks on one side and all the eyes on the other, there is a risk that with movement, the hooks could pop out of the eyes. If you sew them on alternating this does not happen. They are stitched on with a buttonhole stitch with heavy thread. When stitching hooks and eyes or bars, it is important to take at least one small stitch through all the layers to the right side of the garment. This holds all the layers together as one when the hooks are done up.
The centre front is supported on both sides with spiral steel boning to keep it rigid. We also put boning in the garment underneath the trim detailing at the side front, sides and side back. This will keep it looking crisp and uncrumpled over the months to come.