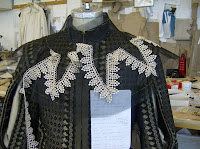
We have a show onstage tomorrow afternoon, and our next show deadline is the 12th of May, so I am doing things like marking alterations on finished suits for actors who have lost weight, and continuing with this project that I've been documenting.
This is the beginning of a large lace collar that will go on this doublet.
I started with draping a collar in muslin with the garment on the stand. At the last fitting, we fit the collar and looked at the overall proportions. At that point I didn't know what kind of lace I would get. I cut the collar base out of a light nylon crin that we have in stock and thread marked the outline of the design. Then the designer brought me some lace and I have pinned it roughly within the design lines. There will be another lace to go into the open area. We will cut away pieces of the lace where required to create a pleasing arrangement of the patterns of the lace.
Now we just have to figure out how to sew it. That task will go to my most experienced team member who has a knack for figuring out the most difficult tasks. I'll show you her samples as she does them, after she finishes the military uniform jacket she is working on.